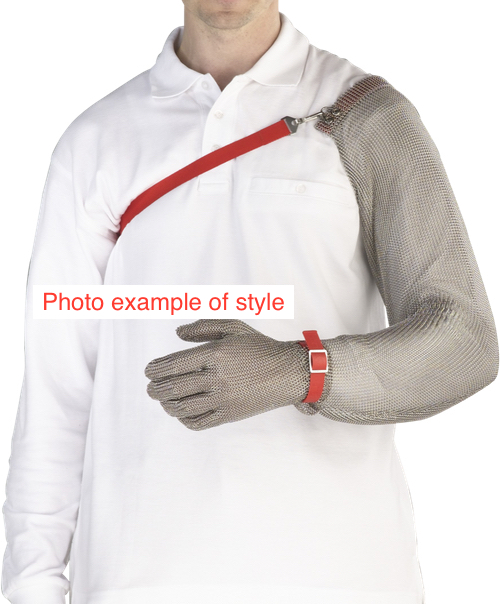
The meat processing industry has always been a high-risk environment and worker safety should be a top priority. One of the most dangerous aspects of this industry is the frequent use of sharp tools such as knives, cleavers, and saws. Ensuring the safety of workers handling these tools has always been a priority, and in recent years, Euroflex gloves have emerged as a game-changer in improving safety standards. Designed specifically to reduce injuries and enhance performance, Euroflex chained gloves are now recognised as essential protective gear across meat processing plants, butchers, and related sectors in the UK.
The Role of Chain Gloves in the Meat Processing Industry
The meat processing industry relies heavily on manual labour for tasks like cutting, deboning, and trimming, all of which involve high-speed work with sharp instruments. Despite safety protocols, accidents such as cuts and lacerations remain common. This is where Euroflex chain mesh gloves step in, offering superior protection through their stainless steel mesh design. Unlike traditional gloves made from materials such as leather or synthetic fibres, chain gloves are specifically designed to withstand the sharpest of blades, minimising the risk of severe injuries.
Key Benefits of Euroflex Chain Gloves
- Unmatched Durability
Euroflex gloves are crafted from high-grade stainless steel, ensuring long-lasting performance. Compared to synthetic gloves that wear out or degrade over time, Euroflex gloves are resistant to wear and tear, maintaining their integrity even under tough conditions in meat processing plants. - Cut-Resistant Protection
The chain mail design provides unparalleled cut resistance. Each metal ring in the mesh absorbs and disperses the force of the blade, reducing the likelihood of punctures or deep cuts. For workers who handle cutting tools day in and day out, this level of protection is crucial in preventing serious injuries. - Hygiene and Sanitation
Hygiene is a critical factor in the meat processing industry. Traditional gloves made from porous materials can absorb bacteria, leading to contamination risks. Euroflex gloves, however, are easy to clean and sanitise, reducing bacterial contamination during meat handling. The stainless steel construction ensures that these gloves can be sanitised using high-temperature processes, keeping both workers and consumers safe. - Comfort and Flexibility
One of the criticisms of early chain gloves was that they were too bulky and hindered movement. These chain gloves, however, are designed to be lightweight and flexible, allowing workers to retain dexterity and precision during intricate tasks such as filleting. The ergonomic design and adjustable straps ensure that workers can perform tasks comfortably for long periods without sacrificing protection.
The UK Market for Industrial Safety Gloves
In the UK, industrial safety standards are among the highest in the world, particularly in high-risk industries like meat processing. The UK industrial safety gloves market has seen a shift toward more advanced protective gear, with chain gloves like those from Euroflex becoming the industry standard. Meat processing companies are increasingly investing in meat processing gloves UK to comply with strict safety regulations and to reduce the number of workplace injuries.
The demand for chain gloves for butchers has also surged as small and medium-sized enterprises (SMEs) in the meat industry realise the importance of worker safety. Not only does it reduce downtime caused by injuries, but it also enhances productivity by boosting worker confidence.
Availability and Accessibility: Finding Euroflex Gloves Near You
For businesses or individual butchers seeking quality safety gear, the search for Euroflex gloves near me has never been easier. With Euroflex’s growing presence in the UK market, both online and physical retailers stock these essential gloves, making them accessible to meat processing plants of all sizes. The gloves are available in different sizes and models, tailored to fit various tasks within the industry, ensuring workers have the best possible protection for their specific roles.
A Case Study: Reducing Injuries at a Major UK Meat Processing Facility
To highlight the effectiveness of Euroflex chain gloves, let’s take a look at a real-life case study of a major UK meat processing facility that faced frequent injury incidents among its workers.
The Problem: Frequent Hand Injuries Impacting Productivity
At a large meat processing plant in northern England, worker injuries had become a significant concern. The facility employed over 500 workers, most of whom were involved in high-risk tasks like cutting and deboning. Despite the use of standard industrial gloves, the company reported an average of 20 hand injuries per month, ranging from minor cuts to severe lacerations requiring medical attention. These injuries not only impacted the well-being of the workers but also led to a loss of productivity due to downtime and worker absenteeism.
The Solution: Implementing Euroflex Chain Gloves
After assessing the situation, the management team decided to invest in Euroflex chain gloves for all workers handling cutting tools. The gloves were introduced gradually across various departments, and workers were trained on how to wear and maintain them properly. Within three months, the facility saw a dramatic reduction in hand injuries. In fact, the number of reported injuries dropped from 20 incidents per month to just 2 minor cuts, which did not require medical intervention.
Additionally, worker morale improved as employees felt safer and more confident in performing their tasks. The plant’s productivity increased, and the company noted that the initial investment in Euroflex mesh gloves paid off in the form of fewer insurance claims and reduced medical costs associated with workplace injuries.
The Impact on Long-Term Safety Culture
The introduction of Euroflex chain gloves didn’t just resolve an immediate safety issue; it also contributed to a long-term shift in the company’s safety culture. Management and staff became more aware of the importance of using high-quality protective gear and adhering to safety protocols. The success of the Euroflex gloves led the facility to invest in additional protective equipment for other high-risk tasks, further enhancing worker safety.
The Future of Euroflex Chain Gloves in the Meat Processing Industry
As the meat processing industry continues to evolve, the importance of worker safety will only grow. With advancements in technology and material science, Euroflex continues to innovate, producing gloves that offer even greater protection without sacrificing comfort. The rise in demand for UK industrial safety gloves reflects an increasing awareness of the importance of worker protection, particularly in sectors where sharp tools are used daily.
Furthermore, the versatility of Euroflex gloves means they are now being adopted in other industries where cut resistance is essential, such as the food processing and packaging sectors. With a reputation for durability, hygiene, and superior protection, Euroflex is positioned to become the global leader in industrial safety gloves.
Conclusion: Why Euroflex Chain Gloves are Essential for Meat Processing
For businesses in the meat processing industry, investing in high-quality protective gear like Euroflex chain gloves is not just a matter of compliance with safety regulations—it’s about safeguarding the health and well-being of workers. The meat processing gloves UK market continues to grow, and Euroflex remains a top choice due to its proven track record of reducing injuries and improving productivity.
Whether you’re a large-scale meat processing plant or a local butcher searching for chain gloves for butchers, Euroflex offers the durability, comfort, and protection needed to keep workers safe. By investing in Euroflex gloves near me, businesses can ensure a safer, more productive work environment, where injuries are minimised and employees can work with confidence.
In today’s industry where safety and precision go hand in hand, Euroflex chain gloves are not just making a difference—they’re changing the way businesses protect their most valuable asset: their workers.